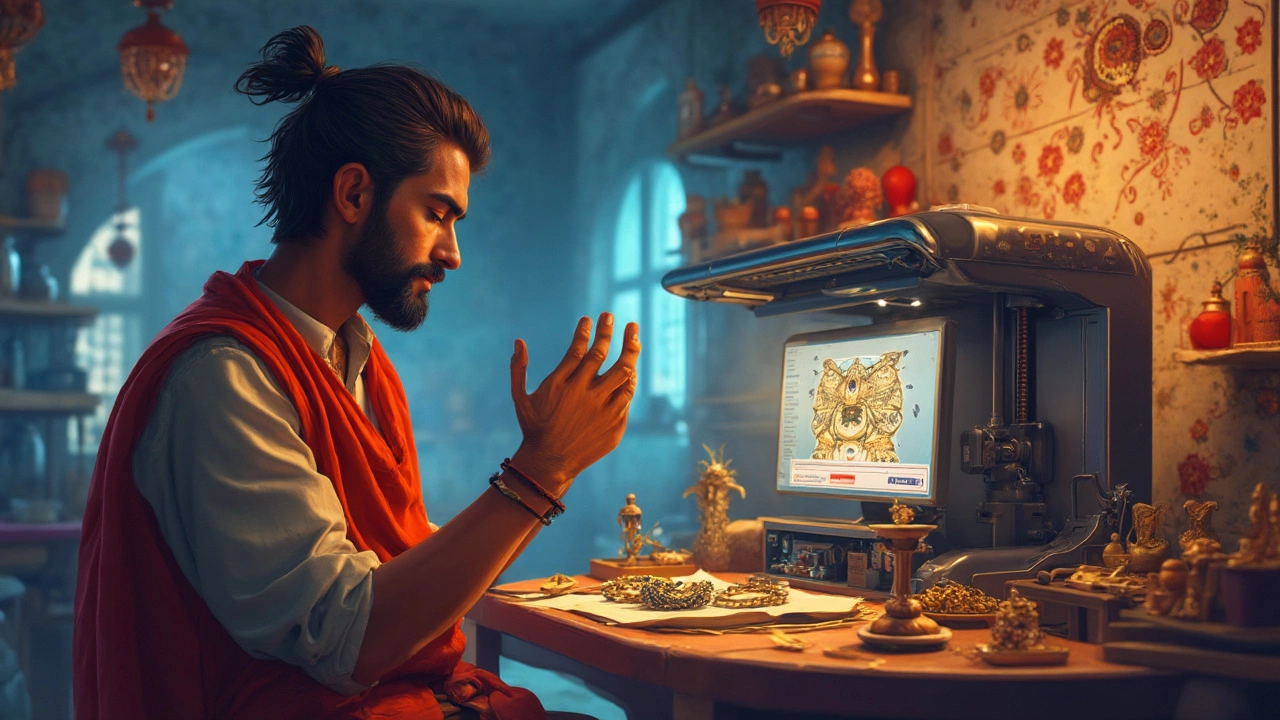
So, you're excited about diving into the world of jewellery making with 3D printing kits? Who wouldn’t be! This tech promises all sorts of creative possibilities. But before you jump in, it's worth knowing there are some hurdles to watch out for.
First off, the materials. Unlike traditional methods where jewellers have a broad palette of metals and stones to play with, 3D printing in jewellery is a bit limited. Many printers can't handle metals at home, so folks often end up working with plastics or need to outsource metal parts, which might not capture the beautiful finish you're aiming for.
Material Limitations
When it comes to 3D printing in jewellery making, the excitement often hits a reality check with material limitations. Let's break it down a bit, shall we?
Types of Materials
Most common 3D printers used at home typically support materials like plastics, specifically PLA and ABS. While great for preliminary designs, they definitely aren't winning any awards for luxury or durability. If you were dreaming of whipping up something in gold or silver right at your desk, that's a bit of a stretch.
For those adamant about using metals, you're mostly looking at a much higher-end equipment or outsourcing to professional printing services. That's where costs can start climbing, and it's not just the price of the machine but also the maintenance and specific powders or filaments required for metal printing.
Quality of Output
It's not just about the types of materials, but also how they look. Plastics, for example, might leave you with a product that lacks the sheen and finish of traditional jewellery. And with metal, even if you do manage to print it, the resolution often can't match traditional craftsmanship, which could leave fine details looking fuzzy.
- Detail Differences: High-detail designs might lose their finesse when translated into certain 3D printing materials. Always check the specifications of your printer before starting a detailed project.
- Post-processing Needs: Be prepared for some post-printing polish work, especially when working with resins or metals to achieve that desirable jewellery finish.
Ultimately, while 3D printing opens doors to creativity, it's vital to be aware and prepared for its material limitations. Being strategic about design and knowing when a traditional method may better serve your ideas can be a game-changer in jewellery crafting.
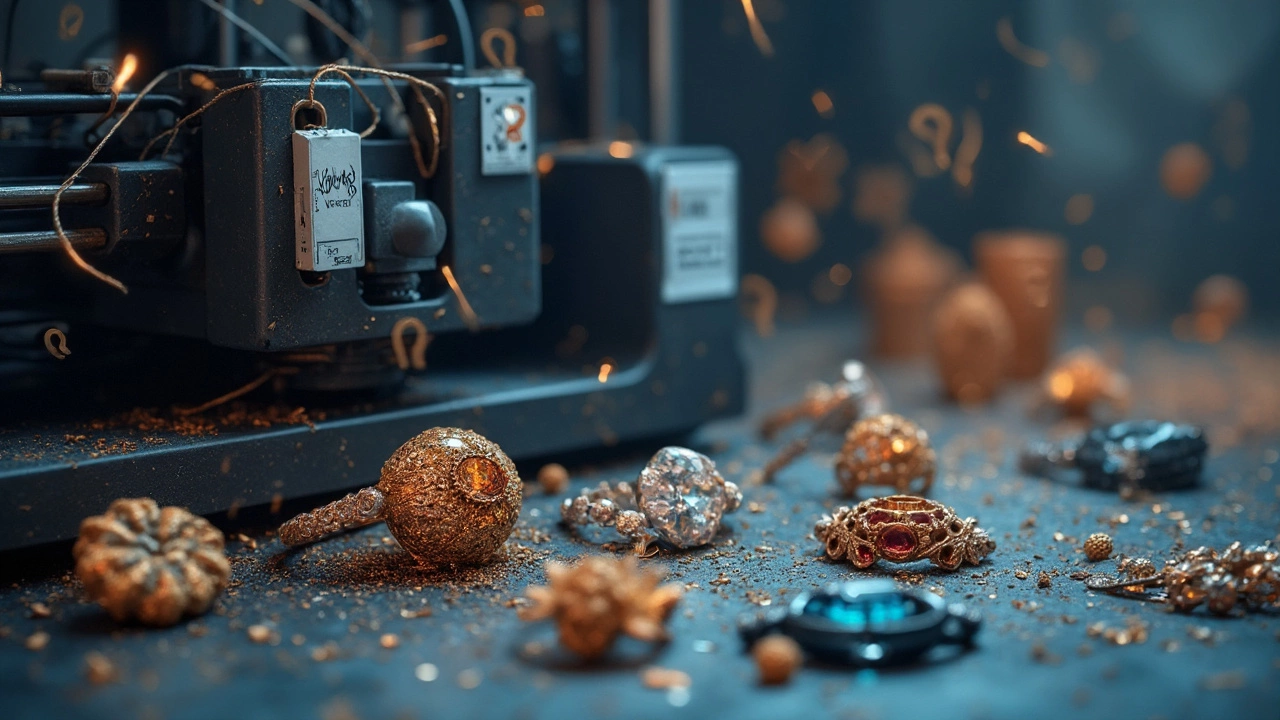
High Costs and Accessibility
Diving into the world of 3D printing for jewellery making can be like opening Pandora's box of costs. For starters, the printer itself isn't cheap. If you want something that can handle detailed designs and quality finishes, you're looking at serious money upfront. A decent printer can set you back anywhere from a few hundred to several thousand dollars.
Then there's the software. While some entry-level software is free, more advanced, feature-rich ones may require subscriptions or one-time purchases. These costs add up, and that's before considering the raw materials like resins or filaments, which aren't always as budget-friendly as you might hope.
Maintenance and Upgrades
Once you've got your setup, there's the ongoing maintenance. Repairing a 3D printer isn't exactly like fixing your toaster; it can be specialized and costly. Replacement parts, regular upkeep, and potential upgrades as technology evolves keep the financial faucet running.
Accessibility for Beginners
For newbies, the accessibility factor can feel like walking into a maze without a map. Not everyone has easy access to in-depth training or support, making the learning curve steep. Online communities and resources are growing, thankfully, but navigating this space can still feel daunting for some.
And let's not forget about the accessibility of materials. While advanced users might dare to experiment with different materials, beginners might find themselves stuck in a rut of basic options due to unavailability or prohibitive costs.
Cost Comparison Table
Component | Low-End Cost | High-End Cost |
---|---|---|
3D Printer | $300 | $5000+ |
Software Subscription | Free | $500/year |
Materials | $20/kg | $150/kg |
So, while 3D printing offers dazzling potential, weighing the costs and accessibility issues is key. For many, the question isn’t just how to start, but whether starting makes sense given these factors.
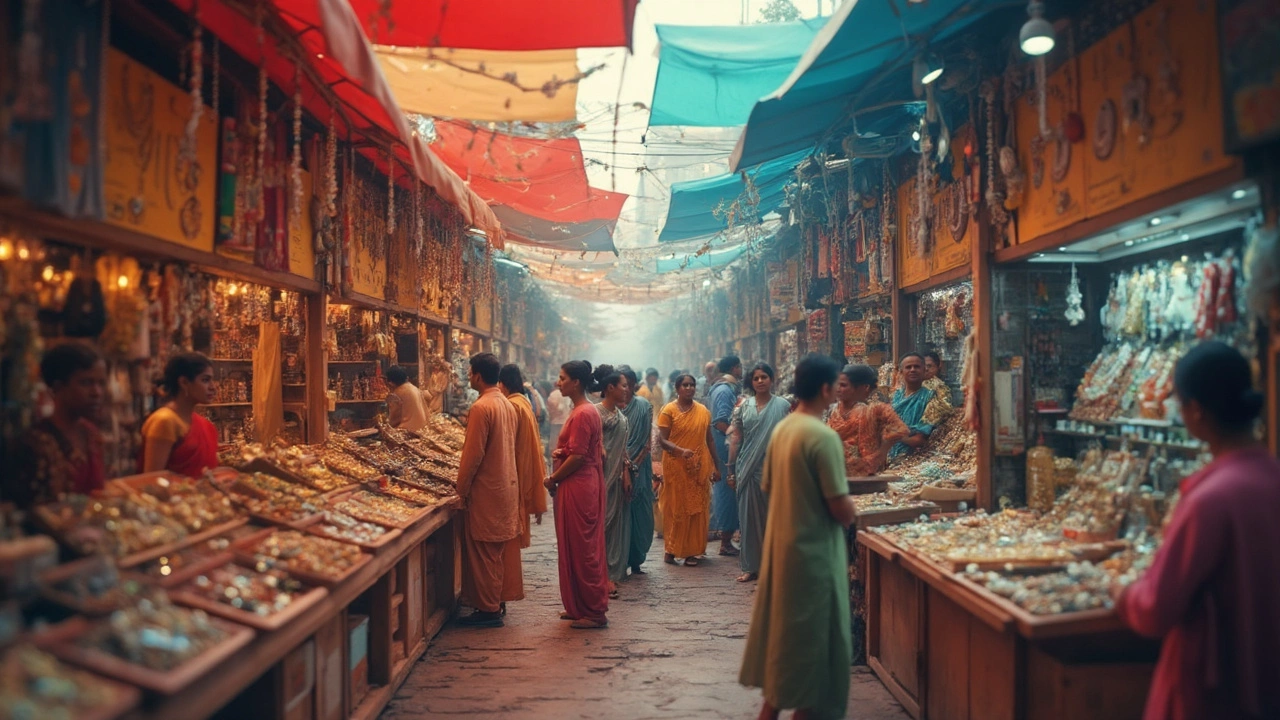
Design Complexity and Time Consumption
When it comes to 3D printing in jewellery making, you might find design complexity both a blessing and a curse. The ability to create intricate designs is undoubtedly a game-changer, but it also brings along some hefty challenges.
First, let's talk about software. Creating detailed models requires mastering CAD (computer-aided design) software, which can have a steep learning curve. Not everyone's a tech wizard, and wrestling with these programs can be time-consuming.
Even after you nail the design, printing itself isn't exactly swift. Depending on the complexity of your piece, printing can take hours to complete. Need multiple pieces? Better block out a good chunk of your day. This isn't akin to instant coffee, folks.
Potential Design Errors
Another hiccup is the potential for design errors. One tiny mistake in your digital model can mean the difference between a stunning piece and a ruined print job. And redoing a print means resetting the clock, which can be frustrating if you’re on a tight schedule.
Post-Processing Time
Once you've got your printed piece, think you're done? Not quite. Many prints need post-processing to get them polished and presentable, adding more time to the process. This can include sanding, cleaning, and even painting, depending on your initial material choice.
Time vs. Convenience
Despite these drawbacks, some enthusiasts find the trade-off fair for the customization level and creative control 3D printing offers in jewellery making. It's all about managing expectations and knowing you’re trading some time for unique, personalized pieces.