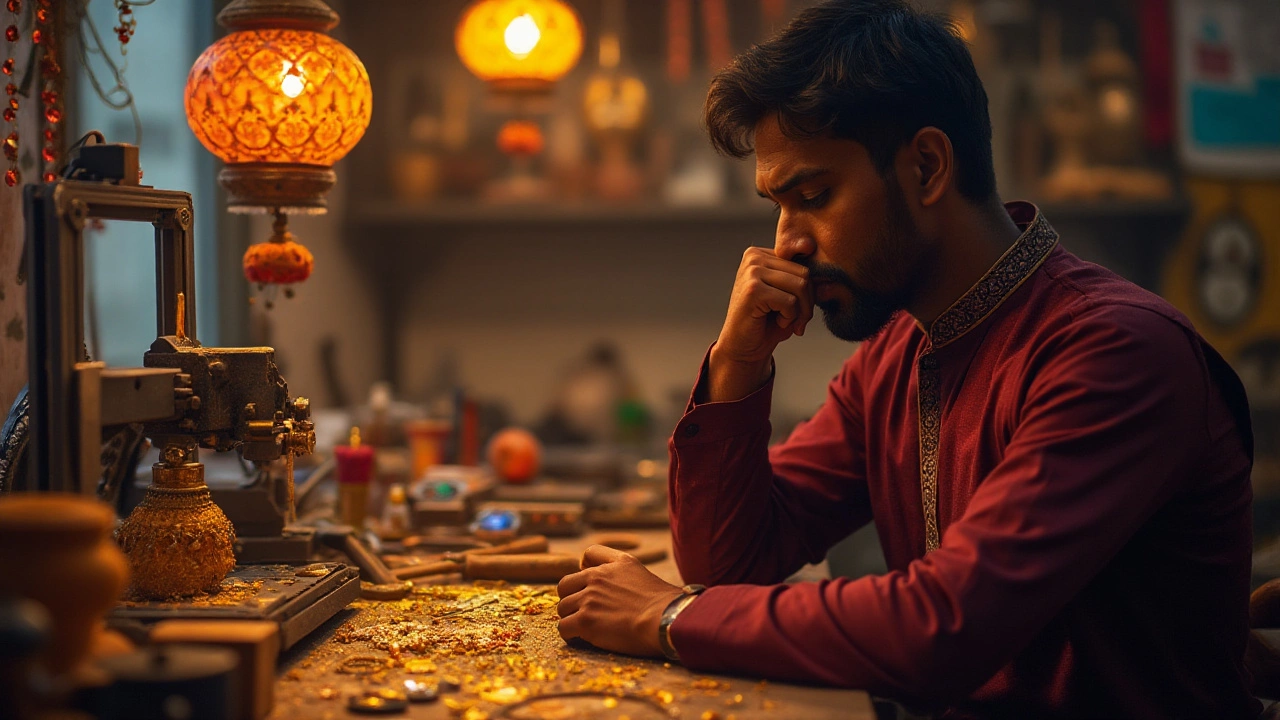
The world of 3D printing has transformed the jewelry making industry by giving artists and designers the freedom to create intricate designs that would be expensive or impossible with traditional methods. Yet, as revolutionary as this technology is, it comes with its own set of limitations, particularly when it comes to the types of metals you can use. Some metals simply don't play nice with the 3D printing process due to their physical and chemical properties.
In this exploration, we'll dive into the complex relationship between 3D printing technology and the metals used within it. Understanding why certain metals are unsuitable for 3D printing can not only save you time and resources but also refine your creative process when designing unique jewelry pieces. We’ll take a closer look at these metals and decode why they resist the embrace of modern printing technology, ensuring your ventures into jewelry-making are both innovative and practical.
- Understanding 3D Printing in Jewelry
- Metals Commonly Used in 3D Printing
- Why Certain Metals Can't Be 3D Printed
- The Challenges of Printing with Unfriendly Metals
- Future Trends in 3D Printing and Jewelry Making
Understanding 3D Printing in Jewelry
In recent years, the fusion of technology and artistry has changed jewelry-making forever, with 3D printing at the forefront of this revolution. Unlike traditional methods, where artisans meticulously craft each piece by hand or with molds, 3D printing enables the creation of complex geometries that push the boundaries of design. This leap into the digital realm means anyone with a creative spark and a computer can transform their ideas into tangible works of art, using metals and other materials. But not just any process will do, as 3D printing involves layering materials based on a digital model to form objects with precision and speed.
The typical 3D printing process involves a few key steps. First, designers craft a digital model using CAD (Computer-Aided Design) software, meticulously drafting each curve and detail. This digital blueprint is then sliced into layers, ready for the printer to interpret and construct. As the printer lays down each layer, it forms the piece from the ground up, usually in a few hours, depending on complexity. The range of materials available for this technology is astounding, from plastics to ceramics, and of course, metals which are particularly interesting for jewelry makers.
Among the metals commonly utilized in 3D printing, you’ll find gold, silver, and platinum leading the charge. But it’s not just the allure of precious metals drawing jewelry makers to this method; there's also the ability to work with unconventional materials like titanium and stainless steel, offering a modern twist on classical designs. The very nature of 3D printing metals revolves around Selective Laser Melting (SLM) and Direct Metal Laser Sintering (DMLS), which selectively target metal powders, fusing them into a unified structure. This process, while ingenious, demands a keen understanding of metallurgy and temperature control to avoid imperfections that could compromise the integrity of the jewelry.
However, the journey isn't straightforward. Experts in the field, like Jessica Rosenkrantz, co-founder of a leading 3D printed jewelry company, emphasize the transformative nature of this technology, stating,
"3D printing aligns perfectly with jewelry design because it allows for the personalization and customization that the jewelry industry thrives on."This sentiment captures why designers are enamored by the technology: the opportunity to produce one-of-a-kind items tailored to the whims of individual customers. The ability to iterate designs quickly and produce prototype after prototype without the overhead costs of traditional methods is a game-changer for new designers entering the market.
The impact of 3D printing in jewelry extends beyond production efficiency. It enables sustainability by minimizing waste material compared to traditional casting techniques. The use of recycled metals is also becoming prevalent as designers seek eco-friendly approaches to their creations. This paradigm shift isn't just technical but also philosophical, as creators ponder over how they can produce beautiful items without taxing the planet's resources inconsolably. It appears the future of jewelry is not just shiny, but also green, thanks to these advances.
Looking ahead, the future of 3D printing in jewelry appears as bright as a diamond’s sparkle. Researchers and developers continue to refine the technology, aiming to introduce even more exotic metals and composite materials into the mix. The newfound ability to incorporate textures, gradients, and even intricate internal structures right within the design phase means that there are virtually no limits to what can be achieved. As with any cutting-edge technology, the cost of 3D metal printers is expected to decrease over time, making it accessible to smaller artisanal businesses and opening up opportunities to innovate on a grand scale.
Metals Commonly Used in 3D Printing
3D printing, also known as additive manufacturing, has revolutionized the creation of intricate jewelry pieces by offering unrivaled precision and customization. But to unlock its full potential, one must navigate the world of metals, as not all metals are created equal. Metals like silver and gold often find favor due to their luster and desired characteristics, but it's the compatibility with 3D printing techniques that truly determines their place in this innovative process.
The advent of technologies such as Selective Laser Melting (SLM) and Electron Beam Melting (EBM) have paved the way for using metals such as titanium and stainless steel in creating durable and detailed pieces. Titanium, revered for its strength and lightweight nature, offers a unique advantage in crafting robust yet delicate designs. Stainless steel, with its wide availability and resilience, provides a more economical option without compromising on quality.
Equally fascinating is the use of aluminum in 3D printing. Known for its excellent corrosion resistance and lightweight properties, aluminum allows for efficient and intricate designs, making it a favorite for both prototypes and finished pieces. Specialists have also begun to explore the use of cobalt chrome, which offers high wear resistance suitable for high-stress applications.
Beyond physical properties, the cost and availability impact a metal's usability in 3D printing. Precious metals like platinum and palladium are used, although less frequently, due to cost constraints. However, their usage is increasing thanks to advances in technology that help reduce waste, therefore lowering costs. As one expert noted,
"Choosing the right metal for 3D printing is comparable to finding the perfect canvas—some are smooth and malleable, while others lend themselves to a technique that ultimately shapes the outcome."
In the realm of jeweler's choice, each metal offers a distinct combination of benefits and challenges. The embrace of 3D printing in the jewelry industry signals an era where design limitations are not just challenged, but altogether departed from, as artisans align creativity with compatible materials. As technology evolves, we are likely to witness an expansion in the roster of metals commonly used, further driving the possibilities in jewelry design and creation.
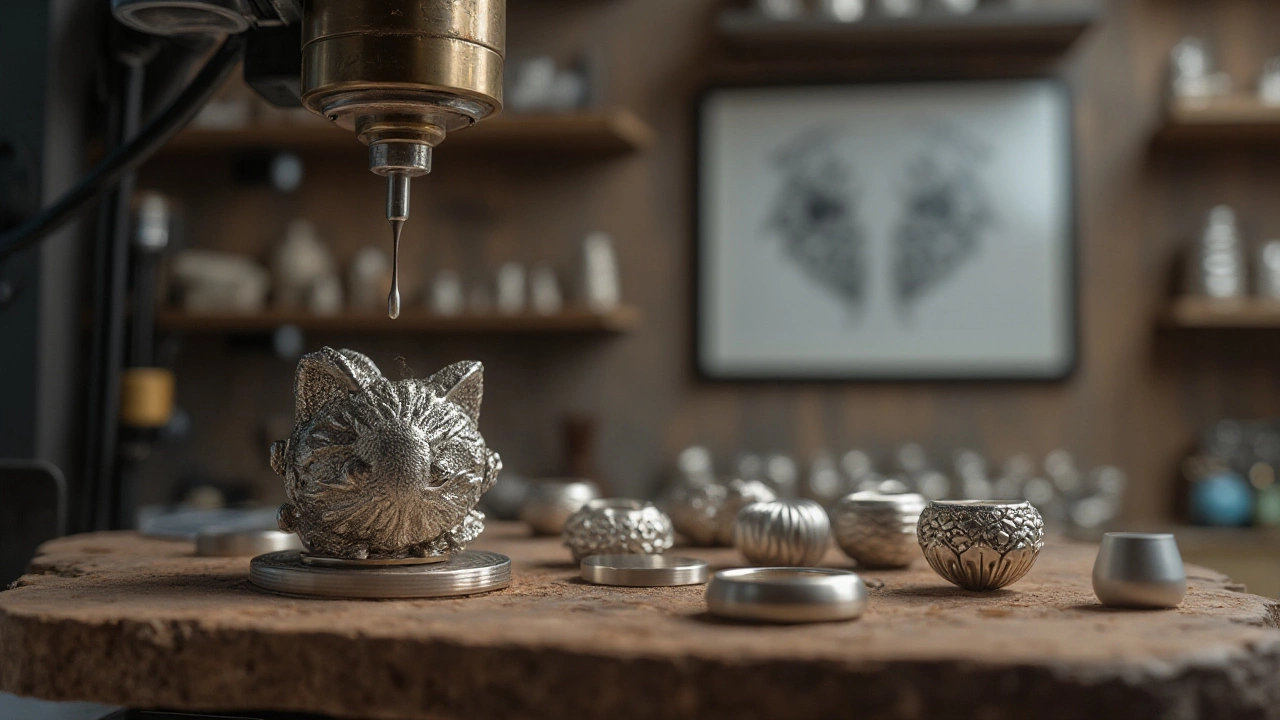
Why Certain Metals Can't Be 3D Printed
3D printing has reshaped the landscape of manufacturing, especially in the dynamic world of jewelry making. However, this technological revolution has its limits, particularly concerning which metals are suitable for this process. Not every lustrous or industrial metal fits perfectly in the realm of 3D printing, primarily due to their intrinsic physical and chemical properties. To understand this, it’s key to delve into the specifics of metal characteristics that impede the 3D printing process.
One of the main barriers comes from the temperature requirements needed to manipulate metals. Metals like tungsten and tantalum have exceptionally high melting points. Tungsten, for instance, melts at a scorching 3,422°C! This makes the cost-effectiveness and practicality of 3D printing at such temperatures quite a challenge. The high heat required for such metals can cause excessive wear and tear on the printing equipment, not to mention the energy demands. Consequently, these factors make them unsuitable for most consumer-grade 3D printing setups.
Another significant obstacle is related to metallurgical characteristics like brittleness. Metals such as beryllium and certain forms of steel possess brittleness or hardness levels that make them prone to cracking during the layer-forming process of 3D printing. This can lead to poor adhesion between layers and result in a final product that is weakened or structurally unsound. The intricacies of bonding these layers effectively require a meticulous control over conditions that isn't always feasible in 3D printing environments designed for metals.
The reactivity of metals with the surrounding environment also plays a role. Take magnesium as an example; it's highly flammable and reactive upon exposure to air, complicating efforts to print it safely or efficiently. This reactivity demands inert atmospheres and specialized handling, adding layers of complexity and cost that make other metals more attractive for 3D printing in jewelry applications.
Metallurgists and material scientists are constantly experimenting and developing novel alloys and techniques to expand the range of printable metals, but the road is not without its hurdles. According to a segment from Additive Manufacturing magazine's recent report, "there's an ongoing effort to identify new alloys that blend desirable traits from typically non-printable metals to achieve 3D printing viability." This field remains one of intense research and potential innovation, hinting at a future where these limitations could be significantly reduced.
The Challenges of Printing with Unfriendly Metals
Diving into the realm of 3D printing in jewelry, one swiftly encounters the daunting hurdles presented by certain metals. These so-called “unfriendly” metals often beguile designers with their allure and potential, yet they pose significant technical challenges when subjected to the 3D printing process. These challenges are rooted in the intrinsic properties of the metals, and understanding these properties is crucial for anyone looking to navigate the complex terrain of 3D printing metals.
One primary issue is the melting point. Metals like tungsten and tantalum boast exceedingly high melting points, which results in complications during the sintering process. This demand for extreme temperatures not only makes them impractical but also economically unviable. Moreover, such high temperatures can lead to equipment degradation and increased energy consumption. Additionally, metals such as lead or cadmium are avoided due to health hazards, as even trace amounts can result in toxic exposure during handling or wearing. These are not just idle concerns but significant barriers to usage in everyday jewelry.
Beyond this, thermal conductivity plays a pivotal role. High thermal conductivity in metals like copper often leads to difficulty in controlling the printing process, as they tend to dissipate heat too quickly, leading to warping and structural instability. This can result in parts that do not meet the desired quality or strength standards. Tackling these issues often requires cutting-edge equipment and precise control measures, which may not be accessible to hobbyists or small-scale jewellers.
Reactivity and Oxidation: A Constant Battle
Reactivity with the environment is another formidable adversary. Metals such as aluminum and magnesium are highly reactive and prone to oxidation, especially in the presence of air and moisture. This presents issues both during the 3D printing process and after the item is created. The surface can degrade, affecting the aesthetic quality of the jewelry and limiting its longevity.Moreover, the intricacies of 3D printing demand that metals possess certain flow and bonding characteristics. Metals that do not cohere well under heat or pressure often produce unsatisfactory results. For instance, the brittleness of some alloys can lead to cracking, a problem exacerbated by the layer-by-layer nature of the printing process. This poses a continuous challenge in maintaining not only the fidelity of original designs but also the structural integrity of the finished product.
"The art and science of crafting intricate designs rest not just in creating, but mastering the materials at hand," notes Dr. Lydia Carter, a material scientist with expertise in additive manufacturing. Such insights draw attention to the delicate balance needed when trying to innovate within the constraints of existing technology.
In grappling with these challenges, innovation is key. Researchers and industry professionals are continually exploring novel alloys and modified metals to mitigate these issues. Advances in technology have also opened pathways to hybrid techniques that blend traditional and additive methods, offering potential solutions to 3D print with previously difficult materials. This highlights the ever-evolving intersection of art, science, and technology, with each advancement offering fresh possibilities for jewellers.
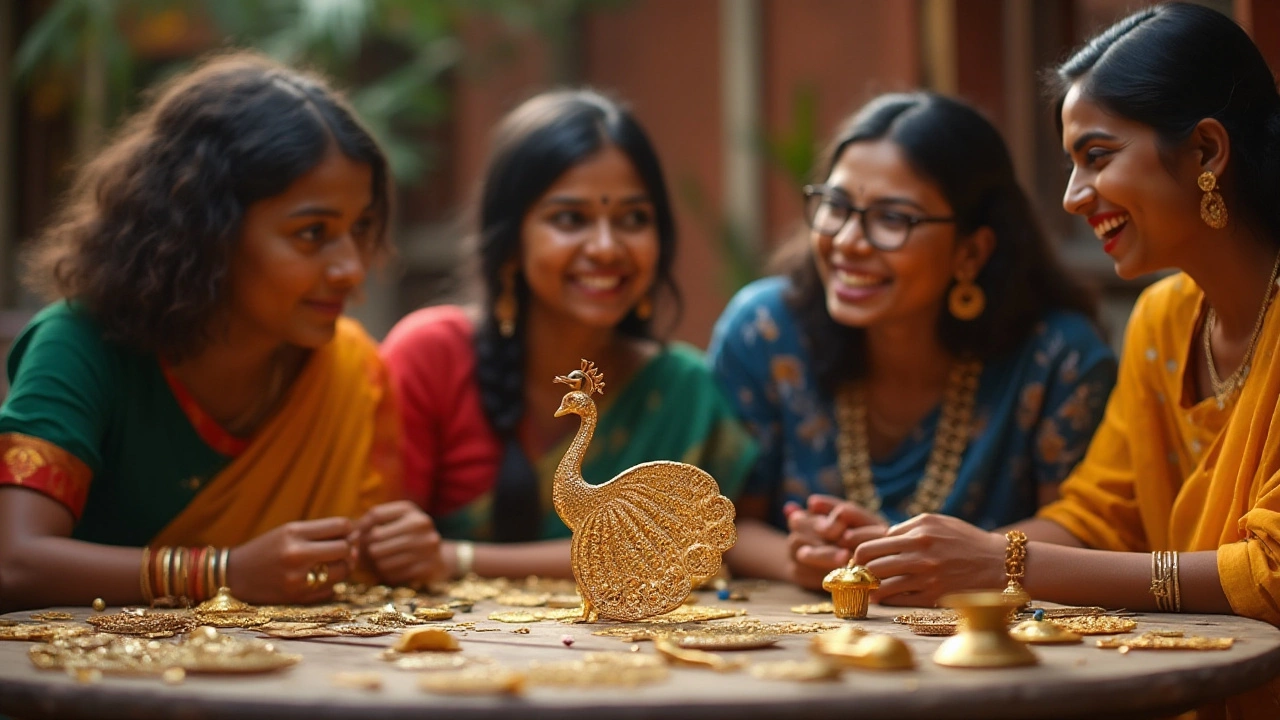
Future Trends in 3D Printing and Jewelry Making
The fusion of 3D printing technology and the art of jewelry making is continually evolving, setting new benchmarks for creativity and innovation. One of the most exciting trends on the horizon is the development of new materials that can overcome current limitations. Researchers and engineers are actively exploring alloys and composites designed specifically for the 3D printing processes used in jewelry. These efforts aim to expand the palette of available materials beyond traditional choices, enabling the creation of previously impossible designs.
As the technology progresses, we are also witnessing a move towards smaller, more precise 3D printers tailored for jewelers. These advanced machines promise higher resolution and improved detail, mirroring the intricate craftsmanship of hand-made jewelry. This trend is empowering independent artisans to compete on quality with larger manufacturers without requiring significant investment in traditional casting equipment. With advancements in 3D printing software, designers now have access to tools that can simulate the casting process, predict potential issues, and allow for virtual prototyping, making the entire workflow faster and more efficient.
"The future of jewelry making lies in a harmonious blend of art and technology, where 3D printing plays a pivotal role in liberating designers from conventional constraints." – Sarah Jordan, renowned jewelry designer
Moreover, sustainability is becoming a central theme in the jewelry industry. The move towards eco-friendly practices includes reducing metal waste and utilizing recycled materials in 3D printing processes. Innovations in this area not only address environmental concerns but also cater to a growing market of consumers who prioritize sustainable products. The ability to print using recycled metals may soon become a standard practice, ensuring that beautiful jewelry pieces contribute to a more circular economy.
Another promising development is the integration of smart technologies within jewelry pieces. As the Internet of Things (IoT) expands, there's potential for creating pieces that are not just beautiful but also functional. High-tech jewelry, embedded with sensors and connectivity features, is likely to become more common, offering features ranging from health monitoring to interactive capabilities. This trend points to a future where jewelry serves purposes beyond aesthetics, enhancing everyday life in remarkable ways.
The educational landscape is also shifting, with more institutions offering courses that marry traditional craftsmanship with 3D printing technology. These courses are crucial in preparing the next generation of jewelers, ensuring they possess the skills to innovate responsibly and creatively. The cross-disciplinary approach empowers young designers to think beyond current possibilities and push the boundaries of what’s achievable with current technologies.
The future of jewelry making through 3D printing is bright and full of potential. As new materials, technologies, and ideas continue to emerge, one can only imagine the incredible designs and innovations that await. The possibilities are as endless as they are exciting, promising a dynamic future where imagination is the only limit.